Understanding Air Pressure Units and Their Applications in Various Industries
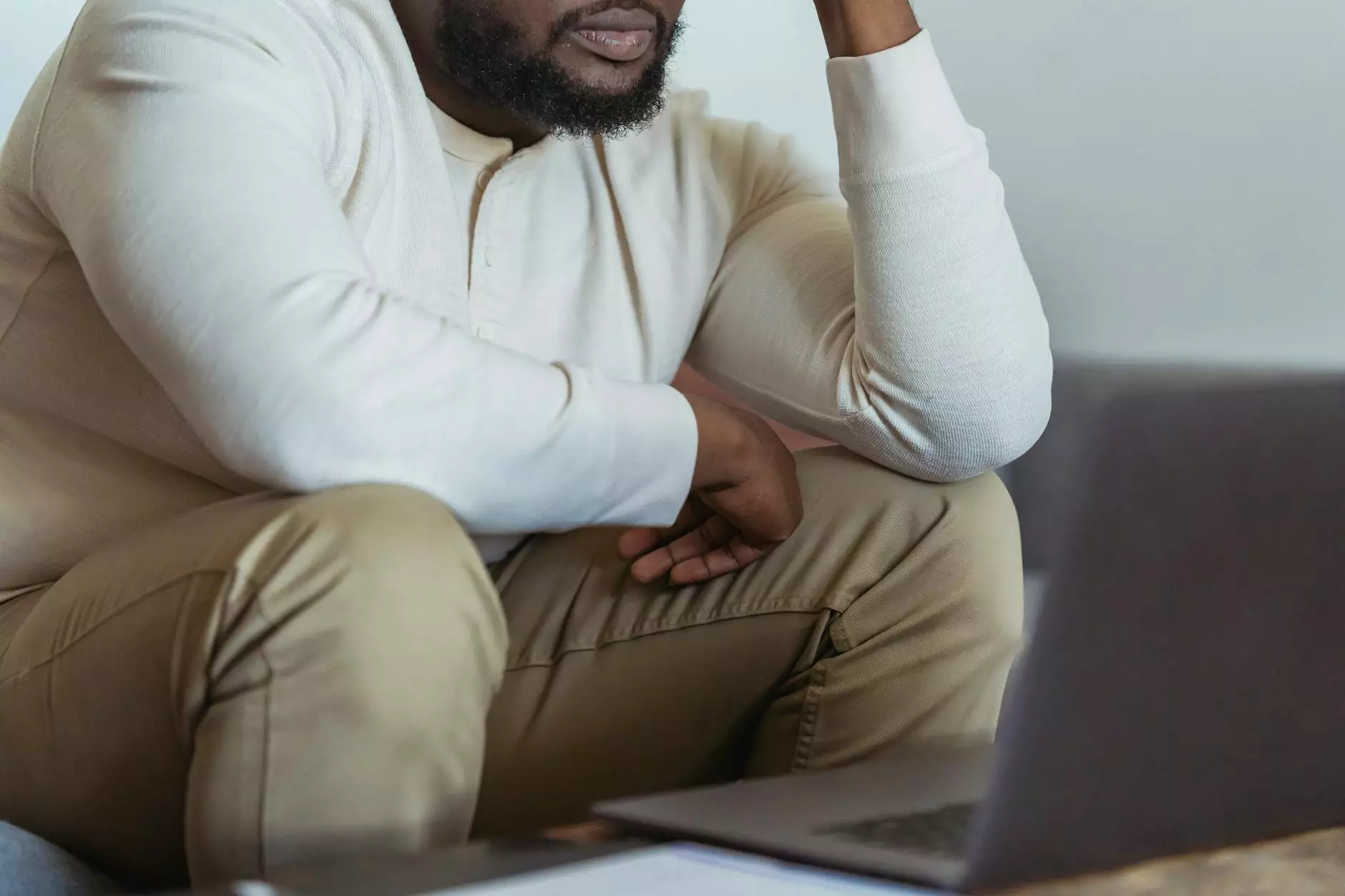
Air pressure units play a vital role in numerous industries, including auto repair, farm equipment repair, and structural engineering. Understanding these units is crucial for both professionals and enthusiasts alike. This article delves into the essence of air pressure units, exploring their importance, measurement, applications, and best practices in various fields.
The Basics of Air Pressure Units
Air pressure is a measure of the force exerted by air molecules against a surface. It is quantified in various units, the most common being:
- Pascals (Pa): The SI unit of pressure, defined as one newton per square meter.
- Atmospheres (atm): Defined as 101,325 Pa, where 1 atm is approximately the air pressure at sea level.
- Pounds per square inch (psi): A non-metric unit commonly used in the United States.
- Millimeters of mercury (mmHg): A unit traditionally used in medicine and meteorology.
Why Are Air Pressure Units Important?
Understanding air pressure is essential for several reasons:
1. Safety and Precautionary Measures
In industries such as auto repair and farm equipment repair, accurately measuring air pressure is critical for safety. Overinflated tires or equipment can lead to dangerous failures. Properly calibrated air pressure units help prevent such incidents.
2. Optimizing Performance
For machinery and vehicles, maintaining the correct air pressure can enhance fuel efficiency and equipment longevity. For instance, farm equipment operating at optimal air pressure will perform better while consuming less energy.
3. Quality Control
In structural engineering, understanding air pressure is crucial for ensuring the integrity of materials and designs. For example, air pressure testing of structures ensures that they can withstand environmental factors, contributing to their durability.
Measurement of Air Pressure Units
The measurement of air pressure can be done using various instruments:
- Barometers: Commonly used to measure atmospheric pressure, useful in weather forecasting.
- Manometers: Often used in laboratories to measure pressure in gases and liquids.
- Digital Pressure Gauges: Provide precise measurements and can be connected to computers for monitoring.
- Vacuum Gauges: Measure pressures below atmospheric levels, important in various engineering applications.
Air Pressure Units in Auto Repair
In the auto repair industry, air pressure units are critical for several applications:
Tire Pressure Monitoring
Correct tire pressure is essential for safety and performance. Most passenger vehicles recommend a tire pressure between 30-35 psi. When tires are under or over-inflated, it can adversely affect handling, fuel efficiency, and tire lifespan.
Air Tools Usage
Air pressure units also dictate the performance of pneumatic tools. These tools operate best within specific pressure ranges, usually between 90 and 120 psi. Regular checks ensure that tools such as impact wrenches and air ratchets function effectively.
Engines and Performance Parts
In modifying engines for performance, maintaining appropriate air pressure in systems such as turbochargers is vital. A common mistake is exceeding the recommended pressure, which can lead to catastrophic engine failures.
Air Pressure Units in Farm Equipment Repair
Air pressure is particularly important in the field of farm equipment repair. Here’s how it impacts operations:
Optimal Tire Pressure for Equipment
Farm machinery such as tractors and combine harvesters require well-maintained tires. The right air pressure around 20-30 psi can help in reducing soil compaction, promoting better crop yield.
Pneumatic Systems in Agriculture
Many agricultural tools use pneumatic systems that depend on precise air pressure to function correctly. This includes seeders and sprayers that utilize compressed air for optimal distribution and performance.
Air Pressure Units in Structural Engineering
In structural engineering, air pressure units have various applications:
Pressure Testing for Structural Integrity
Engineers often employ air pressure testing to assess the integrity of structures. This includes testing the airtightness of buildings, which is crucial for energy efficiency and indoor comfort.
HVAC Systems
Understanding air pressure units is vital in designing efficient heating, ventilation, and air conditioning (HVAC) systems. Proper air pressure ensures better airflow and energy efficiency, impacting overall building performance.
Best Practices for Utilizing Air Pressure Units
To maximize the benefits of air pressure units across various industries, consider the following best practices:
- Regular Calibration: Ensure that pressure measuring devices are regularly calibrated for accuracy.
- Routine Maintenance: Keep all machinery, particularly those relying on pneumatic systems, well-maintained to avoid performance issues.
- Education and Training: Workers should be trained in the importance of air pressure and how to measure it accurately to minimize risks.
- Adhere to Safety Standards: Always follow industry-specific guidelines for safe air pressure levels and practices.
Conclusion
In conclusion, understanding and effectively utilizing air pressure units is crucial across multiple sectors, including auto repair, farm equipment repair, and structural engineering. By maintaining optimal air pressure levels, businesses can ensure safety, enhance efficiency, and improve performance. Whether you are a professional mechanic, a farmer, or a structural engineer, knowledge about air pressure and its measurement is an invaluable asset that can lead to better outcomes in your work. Embrace the significance of air pressure units, and watch how it transforms your operations.
For more information about enhancing your operations through proper air pressure management, visit Michael Smith Engineers.